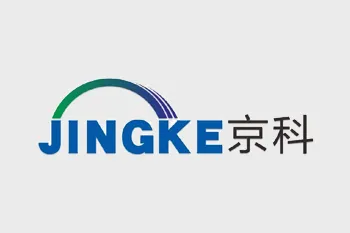
Inspection of stainless steel pipe cutting machine
1. Surface pretreatment of stainless steel pipe cutting machine:
The surface oxide scale and other impurities are removed by sandblasting, and the outer surface of the elbow reaches the Sa2 level specified by the standard.
2. Non-destructive testing:
1) 100% UT or RT inspection shall be carried out for each elbow welding seam, and RT inspection shall be carried out for the repaired welding seam. Comply with the requirements of the standard.
2) After the groove is prepared, magnetic particle or penetrant testing is performed on the entire nozzle and the 100mm length of the weld at the beginning of the nozzle, and the grade I is qualified.
3) Magnetic particle or penetration testing shall be performed on the 90° arc surfaces on both sides of the outer arc of each elbow pipe, and the depth of the defect shall not be greater than 5% of the wall thickness.
4) For the pipe body within the range of ±45° from the neutral plane where the outer arc side of each elbow is basically constant with the wall thickness, UT is used to inspect the transverse crack defect.
5) According to SY/T6423.5 or SY/T6423.6, perform layered curve detection on the elbow, which meets the requirements of the standard.
6) Residual magnetism: check and demagnetize in accordance with relevant regulations, no more than 15Gs.
3. Appearance inspection of stainless steel pipe cutting machine:
1) There are no cracks, overheating, overburning; no hard spots on the surface;
2) Whether the inner and outer surfaces of the stainless steel pipe cutting machine are smooth, with sharp gaps, delaminations, nicks, scars, cracks, folds, tears, cracks, cracks and other defects.
3) It is not allowed to have a pit with a depth of more than 3.15mm on the pipe body of the stainless steel pipe cutting machine or a pit with a depth of more than 1.5mm on the welding seam, and it is not allowed to repair the dent by hammering.